Grazie alla sua elevata durezza, elevata resistenza, eccellente resistenza all'usura e stabilità chimica, la ceramica al nitruro di silicio mostra un'ampia gamma di prospettive applicative in cuscinetti ceramici, utensili da taglio e materiali strutturali ad alta temperatura. In questo studio, come materia prima è stata utilizzata polvere α-Si3N4 autoprodotta, combinata con Y2O3 e Al2O3 su scala nanometrica come additivi per la sinterizzazione e sfere di nitruro di silicio sono state preparate mediante un processo di sinterizzazione a pressione con un costo relativamente basso. In questo documento è stato discusso l'effetto della temperatura di sinterizzazione sulla densificazione, sulla composizione della fase, sulla microstruttura e sulle proprietà meccaniche delle sfere di ceramica, con l'obiettivo di ottimizzare il processo di preparazione e migliorare le proprietà complete delle sfere di ceramica.
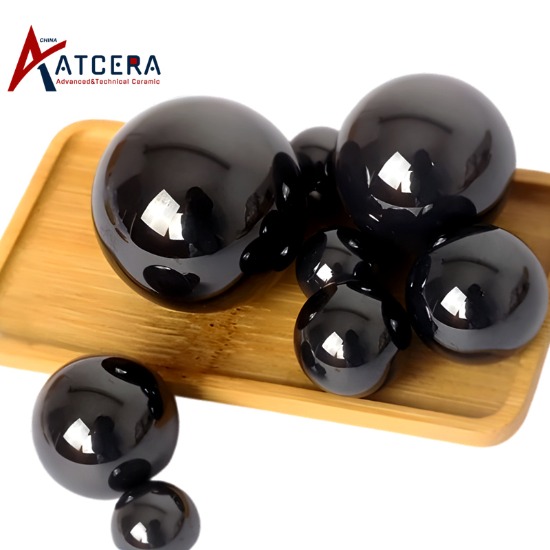
1.1 Materie prime
Le materie prime utilizzate sono polvere di nitruro di silicio (autoprodotta, contenuto di massa α-Si3N4 93%, contenuto di ossigeno <2%, dimensione media delle particelle D50<1μm), ossido di nano-ittrio (reagente sinopyma, purezza 99,9%, mediana dimensione delle particelle D50<100nm), nano-allumina (reagente sinopyma, purezza 99,9%, dimensione media delle particelle D50<100nm). La polvere di nitruro di silicio è stata preparata mediante il metodo di nitrurazione diretta della polvere di silicio, e la sua morfologia microscopica e la composizione di fase sono state mostrate in FIG. 1 e FIG. 2, rispettivamente.
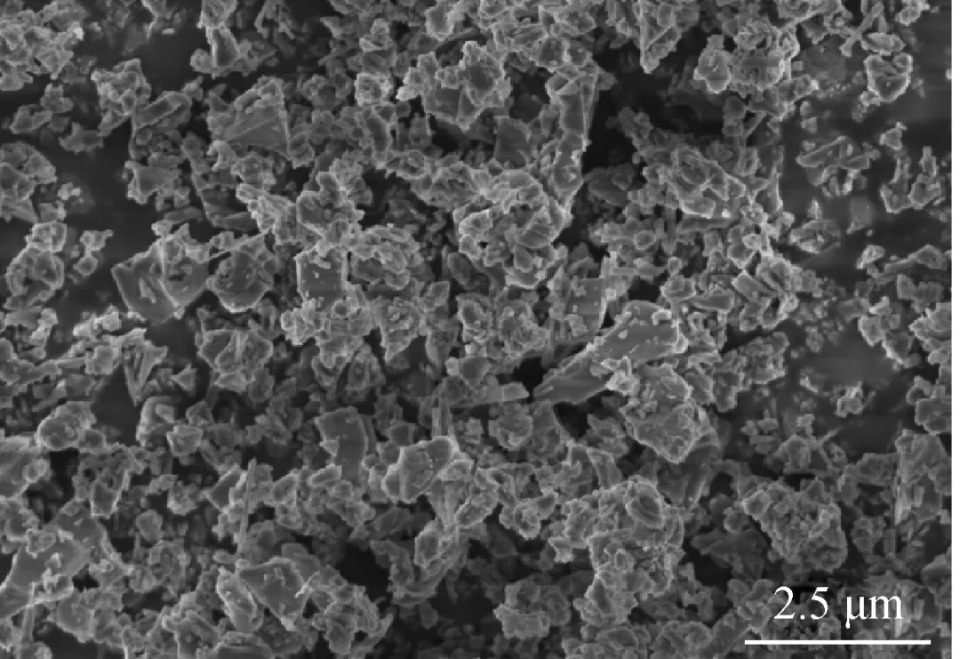
Fig.1 Immagini SEM della polvere di nitruro di silicio
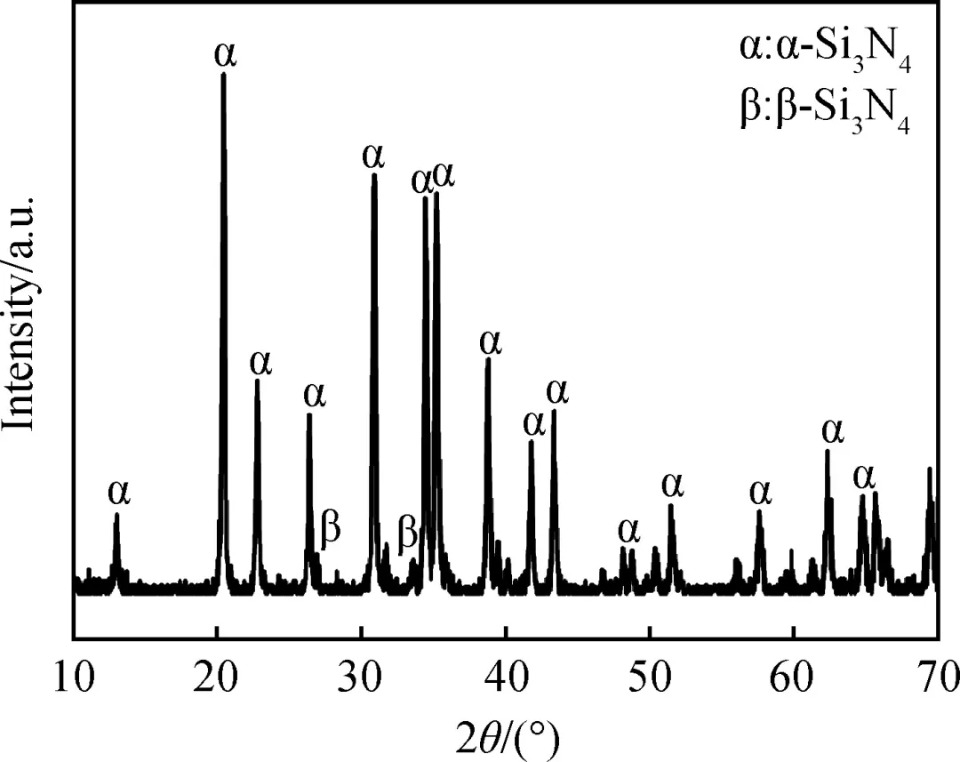
Fig.2 Modello XRD della polvere di nitruro di silicio
1.2 Processo di test
1.2.1 Preparazione del campione
Secondo il rapporto di massa m(Si3N4) â¶m(Y2O3) â¶m(Al2O3)=92 â¶4 â¶4, la polvere di nitruro di silicio e gli additivi per sinterizzazione sono stati aggiunti al mulino a sfere e l'etanolo anidro è stato utilizzato come solvente e la sfera di nitruro di silicio è stata utilizzata come mezzo di macinazione per la miscelazione e la dispersione. L'impasto liquido uniformemente miscelato è stato spruzzato a secco e granulato, e la polvere granulata è stata formata in una sfera di ceramica grezza del diametro di 9,525 mm mediante pressatura a secco e pressatura isostatica a freddo. Il pezzo grezzo di pellet di ceramica è stato mantenuto nell'atmosfera a 500 ℃ per 1 ora per il trattamento di scarico della colla. Dopo lo scarico della colla, il pezzo grezzo di pellet di ceramica è stato inserito nel forno di sinterizzazione a pressione atmosferica per la sinterizzazione a pressione. La temperatura di sinterizzazione era 1720 â, 1750 â, 1780 â, 1800 â, il tempo di mantenimento era di 3 ore e la pressione dell'azoto era di 2 MPa.
1.2.2 Test di analisi
La densità del volume della sfera di ceramica viene misurata mediante il metodo del drenaggio di Archimede e viene calcolata la densità relativa. La formula di calcolo è mostrata nell'equazione (1). Il metodo dell'indentazione è stato utilizzato per misurare e calcolare la durezza Vickers (carico 98 N) e la resistenza alla frattura (carico 196 N) della sfera in ceramica. Il metodo di calcolo della tenacità alla frattura è stato fatto riferimento al metodo proposto da Niihara et al. La formula di calcolo è mostrata nell'equazione (2).
Secondo il metodo di prova a tre sfere previsto dallo standard JB/T 1255-2014, viene testato il carico di schiacciamento della sfera in ceramica e viene calcolata la resistenza allo schiacciamento. La formula di calcolo è mostrata nell'equazione (3).
La composizione di fase dei campioni è stata analizzata mediante diffrattometro a raggi X D8 ADVANCE (XRD). Il microscopio elettronico a scansione a emissione di campo SU8010 (FE-SEM) è stato utilizzato per osservare la microstruttura dei campioni e la dimensione dei grani e il rapporto lunghezza-diametro sono stati misurati sulle foto SEM casuali. Il numero di grani in ciascun gruppo di campioni non era inferiore a 200.

Dove :ρrd è la densità relativa della sfera di ceramica (rispetto alla densità reale),%; ρm è la densità volumetrica della sfera di ceramica,g/cm3; ρesima è la densità teorica della sfera ceramica,g/cm3; ρi è la densità teorica di ciascuna fase,g/cm3; Vi è la frazione di volume di ciascuna fase,%.

Dove IFR è la tenacità alla frattura della sfera in ceramica, MPa·m1/2; E è il modulo elastico della sfera ceramica,GPa, dove E=310 GPa; P è il carico,kgf(1 kgf= 9,8N); a è la lunghezza semidiagonale della rientranza,μm; c è la lunghezza della fessura a mezza punta dell'indentazione,μm.

Dove :σ è la resistenza alla frantumazione della sfera di ceramica,MPa; P è il carico di schiacciamento della sfera ceramica,N; d è il diametro della sfera di ceramica, mm.
2.1 Compattazione
La Figura 3 mostra la densità relativa e i cambiamenti dei campioni di sfere in ceramica di nitruro di silicio dopo la sinterizzazione a diverse temperature. Dalla Figura 3 si può vedere che la densità relativa dei campioni di sfere di ceramica a diverse temperature di sinterizzazione raggiunge oltre il 97% e con l'aumento della temperatura di sinterizzazione, la densità relativa delle sfere di ceramica prima aumenta e poi diminuisce.
Questo perché l'aumento della temperatura di sinterizzazione può ridurre la viscosità della fase liquida, favorire la migrazione delle sostanze e l'esclusione dei pori e accelerare la crescita dei grani, ma la temperatura di sinterizzazione è troppo elevata porterà a risultati anomali crescita dei grani, aggravano la decomposizione del nitruro di silicio e la volatilizzazione della fase liquida, per cui aumenta il numero di micropori all'interno del corpo sinterizzato. Tra questi, la densità relativa dei campioni di sfere di ceramica sinterizzate a 1780 ℃ è la più alta, ovvero il 99%.
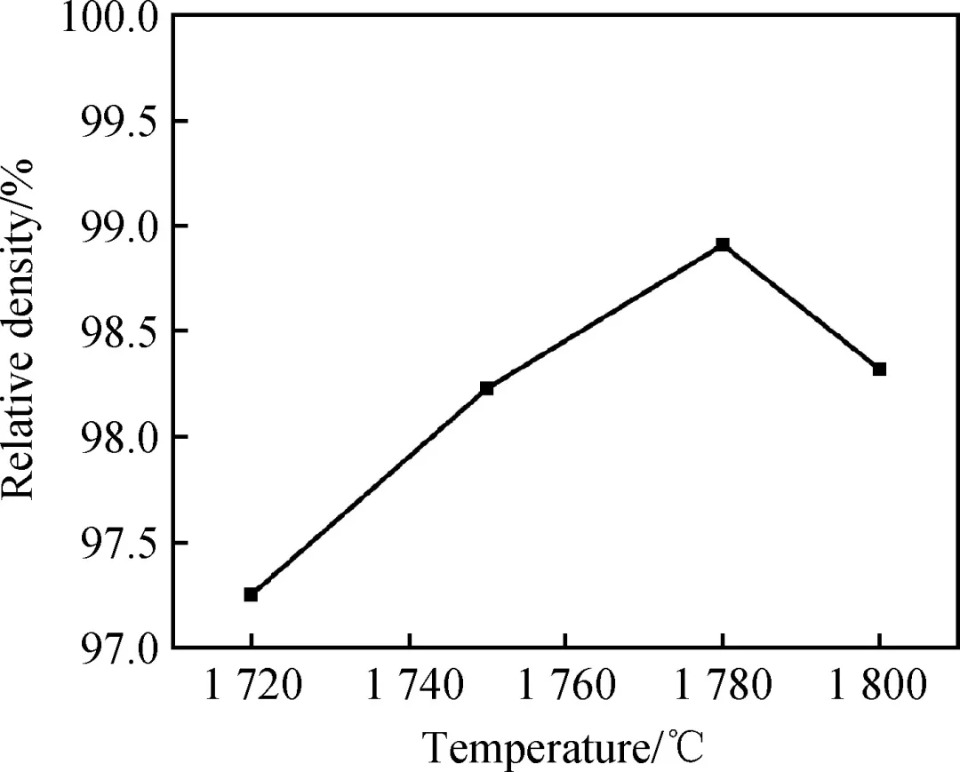
Fig.3 Effetto delle temperature di sinterizzazione sulla densità relativa dei campioni di sfere di ceramica
2.2 Analisi di fase
La Figura 4 mostra gli spettri XRD di campioni di sfere di ceramica a diverse temperature di sinterizzazione. Come si può vedere dalla Figura 4, la composizione di fase dei campioni di sfere ceramiche a diverse temperature di sinterizzazione è la stessa, costituita da β-Si3N4, Si2N2O e Y4Al2O9(YAM), e non viene trovato alcun picco di diffrazione α-Si3N4, indicando che nel 1720 A â e temperature più elevate, α-Si3N4 è stato trasformato in β-Si3N4 e, con l'aumento della temperatura di sinterizzazione, l'intensità del picco di diffrazione di Y4Al2O9 diminuisce gradualmente, il che può essere causato dalla volatilizzazione della fase liquida ad alta temperatura .
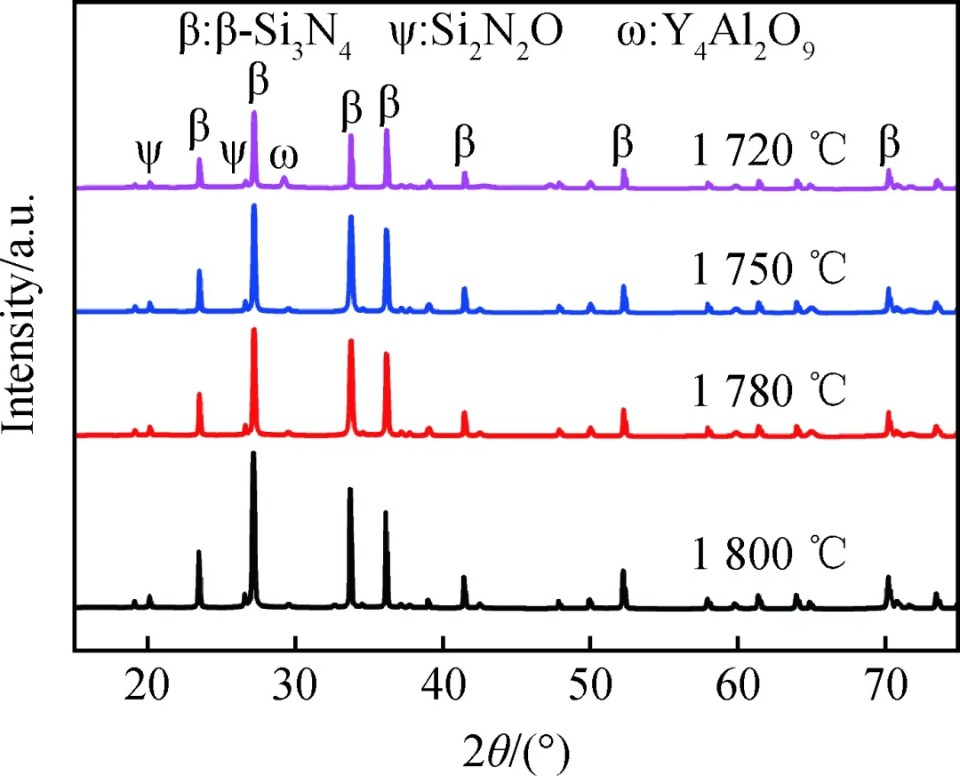
Fig.4 Modelli XRD di campioni di sfere di ceramica sinterizzati a diverse temperature di sinterizzazione
2.3 Microstruttura
FIG. 5 mostra foto SEM di campioni di sfere di ceramica a diverse temperature di sinterizzazione. FICO. 6 mostra i cambiamenti della dimensione del grano (cioè il diametro dei grani colonnari lunghi) e del rapporto lunghezza-diametro del nitruro di silicio secondo le foto SEM.
Si può vedere dalla FIG. 5 e FIG. 6 che la dimensione del grano e il rapporto lunghezza-diametro del nitruro di silicio aumentano gradualmente con l'aumento della temperatura di sinterizzazione. Questo perché la viscosità della fase liquida diminuisce con l'aumento della temperatura di sinterizzazione e la fase liquida con bassa viscosità è più favorevole al trasferimento di massa, che promuove la nucleazione e la crescita dei grani β-Si3N4.
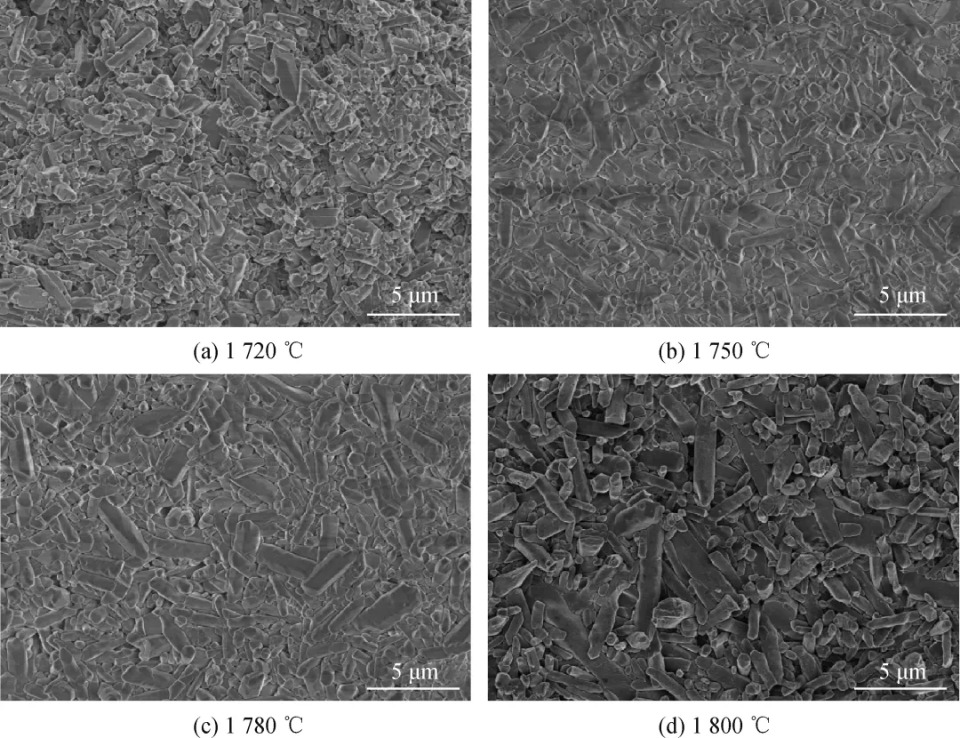
Fig.5 Immagini SEM di campioni di sfere di ceramica sinterizzate a diverse temperature di sinterizzazione
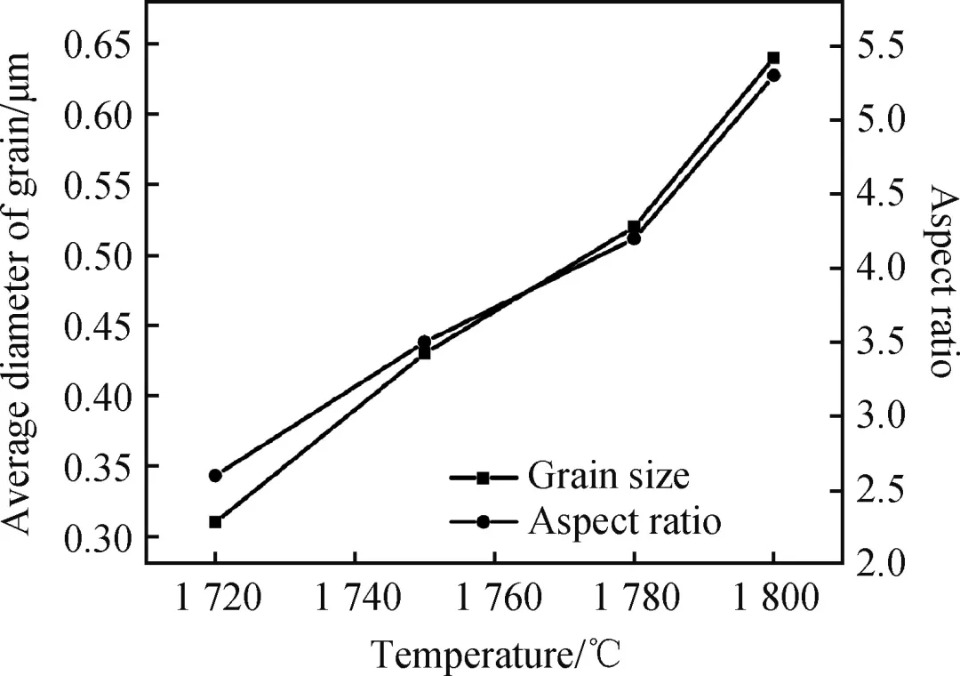
Fig.6 Effetto della temperatura di sinterizzazione sulla dimensione dei grani e sul rapporto di aspetto dei campioni di sfere di ceramica
Tra questi, la microstruttura delle sfere ceramiche sinterizzate a 1720 ℃ presenta molti pori e piccoli grani, che non sono completamente sviluppati, e il rapporto tra lunghezza e diametro è solo 2,6. Le sfere ceramiche sinterizzate a 1750 â e 1780 â hanno microstruttura uniforme, impaccamento compatto dei grani e sviluppo completo, e il rapporto tra lunghezza e diametro è rispettivamente di 3,5 e 4,2. L'uniformità della microstruttura delle sfere ceramiche sinterizzate a 1 800 â è scarsa, sono presenti micropori, ingrossamento dei grani e crescita anomala, il rapporto tra lunghezza e diametro arriva fino a 5,3.
2.4 Proprietà meccaniche
La Figura 7 mostra i cambiamenti della durezza Vickers e della resistenza alla frattura dei campioni di sfere di ceramica a diverse temperature di sinterizzazione. Come si può vedere dalla Figura 7, con l'aumento della temperatura di sinterizzazione, la durezza Vickers della sfera in ceramica prima è aumentata e poi è diminuita, e la tenacità alla frattura ha continuato ad aumentare.
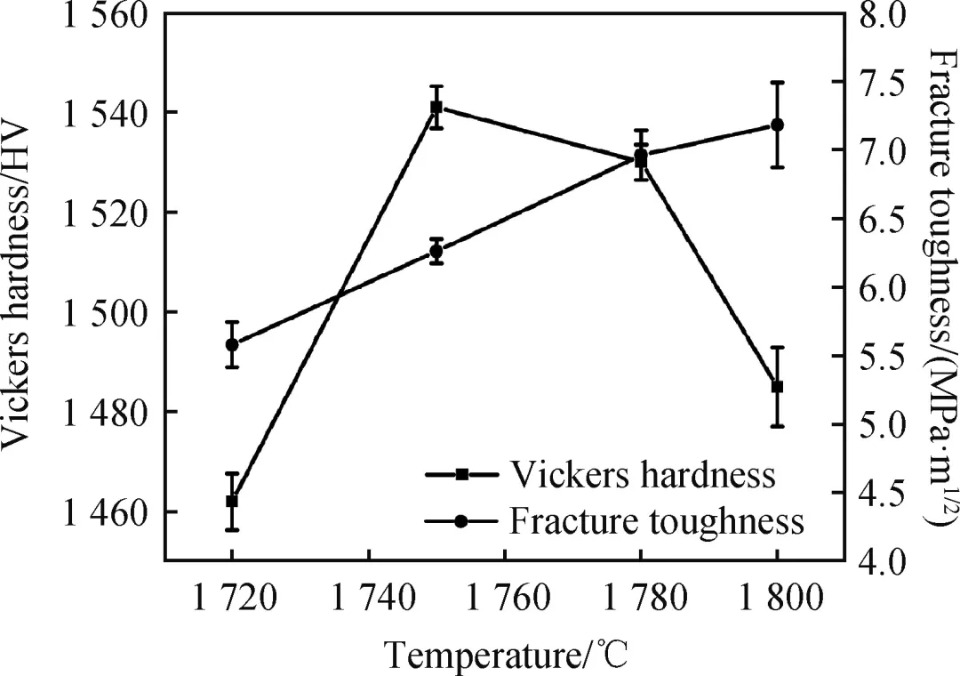
Fig.7 Effetto della temperatura di sinterizzazione sulla durezza Vickers e sulla resistenza alla frattura dei campioni di sfere di ceramica
Quando la temperatura di sinterizzazione è 1720°C, la dimensione del grano e il rapporto lunghezza-diametro delle sfere di ceramica sono più piccoli, la porosità è maggiore e la densità è insufficiente, quindi la durezza Vickers e la resistenza alla frattura sono inferiori. Quando la temperatura di sinterizzazione sale a 1750°C, la dimensione dei grani e il rapporto lunghezza-diametro delle sfere di ceramica aumentano, la densità aumenta e la durezza Vickers e la resistenza alla frattura aumentano rispettivamente a 1540 HV e 6,3 MPa·m1/2.
Quando la temperatura di sinterizzazione è 1780°C, la dimensione del grano e il rapporto lunghezza-diametro delle sfere ceramiche aumentano ulteriormente e la resistenza alla frattura continua ad aumentare, raggiungendo 7MPa·m1/2, ma la durezza Vickers diminuisce leggermente fino a 1530HV.
Quando la temperatura continua a salire fino a 1 800 ℃, i grani delle sfere di ceramica crescono in modo anomalo e sono presenti microfori nella microstruttura, causando un deterioramento della densità, con conseguente forte diminuzione della durezza Vickers. Tuttavia, i grani colonnari lunghi e grossolani possono esercitare la deflessione delle cricche, l'estrazione di ponti e grani e altri meccanismi di indurimento, che migliorano ulteriormente la resistenza alla frattura delle sfere di ceramica.
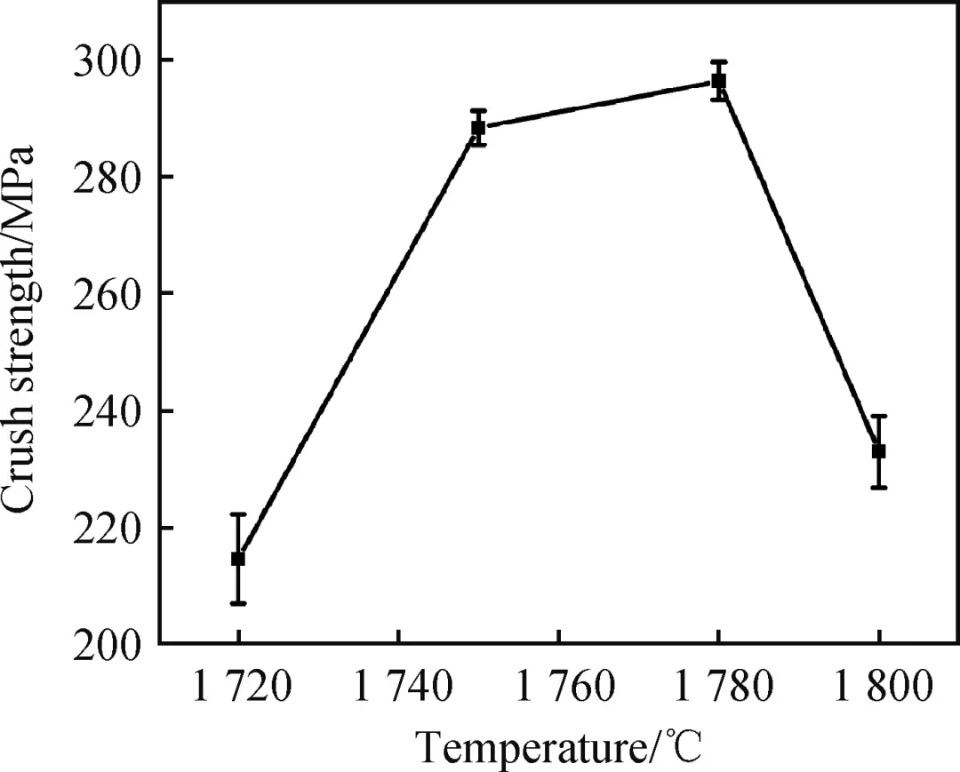
Fig.8 Effetto della temperatura di sinterizzazione sulla resistenza alla compressione di campioni di sfere di ceramica
La Figura 8 mostra la resistenza alla frantumazione e i cambiamenti dei campioni di sfere di ceramica a diverse temperature di sinterizzazione. Come si può vedere dalla FIG. 8, con l'aumento della temperatura di sinterizzazione, la resistenza alla frantumazione della sfera ceramica prima aumenta e poi diminuisce. La resistenza alla frantumazione della sfera in ceramica è influenzata principalmente dalla densità, dalla microstruttura e dai difetti interni. Maggiore è la densità della sfera di ceramica, più uniforme è la microstruttura, minori sono i difetti interni e maggiore è la resistenza alla frantumazione. Tra questi, la resistenza alla frantumazione delle sfere di ceramica sinterizzate a 1750° e 1780° è maggiore, rispettivamente 288 MPa e 296 MPa, indicando che i difetti interni delle sfere di ceramica sinterizzate a queste due temperature sono relativamente pochi.
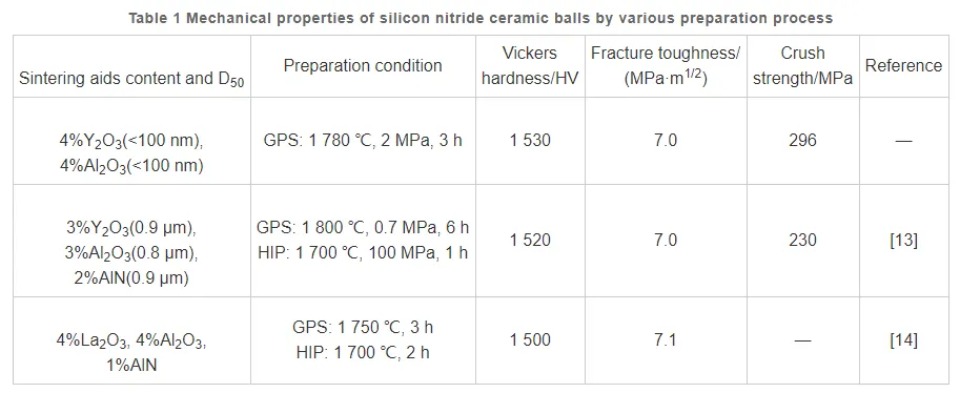
Tabella 1. Proprietà meccaniche delle sfere ceramiche di nitruro di silicio mediante vari processi di preparazione
La tabella 1 mostra il confronto tra le proprietà delle sfere ceramiche di nitruro di silicio preparate mediante processo di sinterizzazione pneumatica e quelle preparate mediante processo di pressatura isostatica a caldo all'estero. Dalla Tabella 1 si può vedere che la durezza Vickers e la resistenza alla frattura della sfera in ceramica di nitruro di silicio preparata in questo test raggiungono lo stesso livello di quella della sfera in ceramica di nitruro di silicio estraneo e la resistenza alla frantumazione è superiore a quella del silicio estraneo sfera in ceramica di nitruro. Poiché l'agente di sinterizzazione utilizzato in questo esperimento è su scala nanometrica, può essere disperso in modo più uniforme nel nitruro di silicio, promuovere la densificazione della sinterizzazione del nitruro di silicio, migliorare la consistenza della dimensione dei grani del nitruro di silicio, quindi le proprietà meccaniche delle sfere ceramiche preparate sono eccellente.
Conclusione
In questo documento, la polvere α-Si3N4 autoprodotta è stata utilizzata come materia prima e Y2O3 e Al2O3 su scala nanometrica sono stati utilizzati come additivi di sinterizzazione per eseguire esperimenti industriali. Sono stati studiati gli effetti della temperatura di sinterizzazione sulla densificazione, sulla composizione della fase, sulla microstruttura e sulle proprietà meccaniche della sfera ceramica di nitruro di silicio per sinterizzazione barometrica. Sono state ottenute le seguenti conclusioni:
(1) Con l'aumento della temperatura di sinterizzazione, la densità relativa della sfera di ceramica aumenta prima e poi diminuisce, e la dimensione dei grani e il rapporto lunghezza-diametro aumentano gradualmente.
(2) Le proprietà meccaniche delle sfere ceramiche in nitruro di silicio sono strettamente correlate alla loro microstruttura e la resistenza alla frattura è influenzata principalmente dalla dimensione del grano e dal rapporto lunghezza-diametro. La tenacità alla frattura aumenta con l'aumento della dimensione del grano e del rapporto lunghezza-diametro. La durezza Vickers e la resistenza alla frantumazione non sono influenzate solo dalla dimensione del grano, ma anche dalla densità e dai difetti interni, quindi con l'aumento della temperatura di sinterizzazione, la tendenza prima aumenta e poi diminuisce.
(3) La sfera in ceramica sinterizzata a 1780° ha le migliori proprietà meccaniche complete, la sua densità relativa raggiunge il 99%, la durezza Vickers, la resistenza alla frattura e la resistenza alla frantumazione sono rispettivamente 1530HV, 7MPa·m1/2 e 296MPa.