La ceramica al nitruro di alluminio è un importante materiale di substrato per la dissipazione del calore, ma il substrato ceramico al nitruro di alluminio in sé non ha conduttività elettrica, quindi la superficie deve essere metallizzata prima di essere utilizzata come substrato di dissipazione del calore ad alta potenza.
La capacità di bagnatura del metallo sulla superficie ceramica ad alta temperatura determina la forza legante tra metallo e ceramica, e una buona forza legante è un'importante garanzia per la stabilità delle prestazioni dell'imballaggio. Pertanto, la realizzazione della metallizzazione del substrato ceramico è una parte importante dell'applicazione pratica della ceramica al nitruro di alluminio.
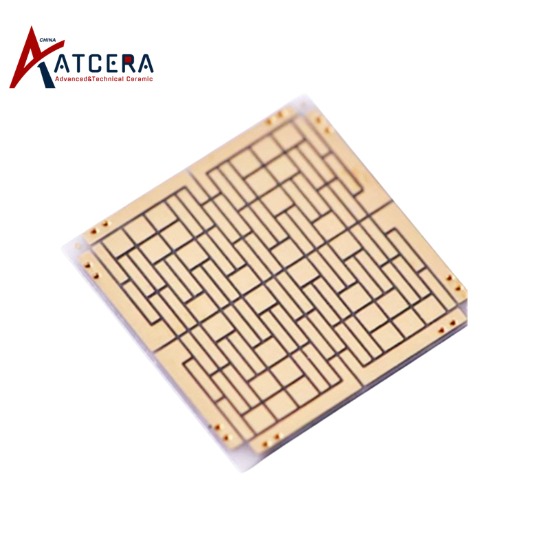
Connessione meccanica e incollaggio
Il metodo di connessione meccanica è caratterizzato dall'adozione di un design strutturale ragionevole e dall'utilizzo di sollecitazioni meccaniche per realizzare la connessione tra il substrato di nitruro di alluminio e il metallo, come la connessione a manicotto caldo e la connessione a bullone. Il metodo di connessione meccanica ha le caratteristiche di un processo semplice e di buona fattibilità, ma lo stress sulla connessione è elevato e non è adatto per ambienti ad alta temperatura e il campo di applicazione è limitato.
Il legame si riferisce al legante organico come mezzo di connessione, attraverso l'appropriato processo di legame, la natura del substrato di nitruro di alluminio e dei materiali metallici combinati in un metodo di connessione meccanica completa. Tuttavia, anche il metodo di incollaggio non è adatto per ambienti ad alta temperatura e alta resistenza e il campo di utilizzo è ridotto.
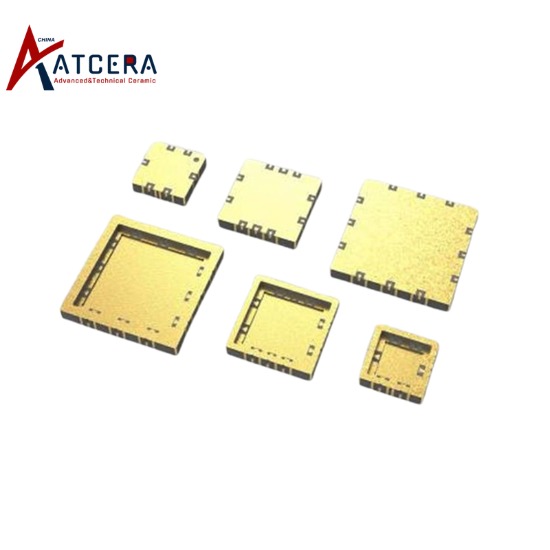
Metodo del film spesso (TPC)
Il metodo a film spesso si riferisce al processo di rivestimento diretto di una pasta conduttiva sulla superficie del substrato ceramico di nitruro di alluminio attraverso la serigrafia, quindi essiccazione e sinterizzazione ad alta temperatura per far aderire il rivestimento metallico alla superficie del substrato ceramico.
La pasta conduttiva è generalmente composta da polvere metallica conduttiva, legante di vetro e supporto organico. La polvere metallica conduttiva determina le proprietà elettriche e meccaniche della pasta dopo la formazione del film, e le polveri metalliche comunemente usate sono argento, rame, nichel e alluminio, ecc., di cui argento e rame hanno bassa resistenza e basso costo e sono più adatto per la produzione industriale.
Pertanto, il processo è affidabile e presenta i vantaggi di un'elevata efficienza produttiva, di un basso costo e di un design flessibile. Il suo svantaggio è che è limitato dalla precisione del processo di serigrafia, l'adesione non è facile da controllare e il substrato sinterizzato non può ottenere linee ad alta precisione, quindi può essere applicato solo a materiali di imballaggio di dispositivi elettronici con linea bassa requisiti di precisione.
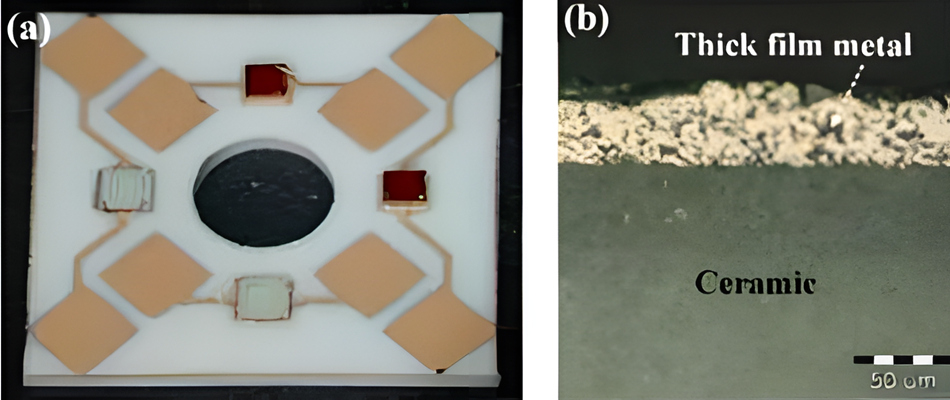
Brasatura attiva dei metalli (AMB)
Il metodo di brasatura del metallo attivo consiste nell'aggiungere direttamente Ti, Zr, Al, Nb, V e altri elementi di transizione con proprietà chimiche relativamente attive nel comune metallo di brasatura. Questi elementi attivi reagiscono chimicamente direttamente con la superficie della ceramica al nitruro di alluminio per formare uno strato di transizione, il prodotto principale dello strato di transizione sono alcuni composti leganti metallici e hanno la stessa struttura del metallo, quindi possono essere bagnati dal riempitivo fuso metallo per formare un giunto metallurgico.
Il substrato ceramico in nitruro di alluminio è un importante dispositivo di dissipazione del calore, spesso utilizzato a temperature elevate, quindi sono necessari più giunti ad alta temperatura. Il metallo per brasatura attivo ad alta temperatura composto principalmente da CuTi e NiTi può essere utilizzato nell'intervallo 1200~1800℃. Il metallo per brasatura con sistema ternario o sistema multicomponente rappresentato da base Au, base Co e metallo per brasatura base PD è il metallo per brasatura attivo ad alta temperatura più comunemente usato. Il punto di fusione di Au, Co e Pd è rispettivamente 1064℃, 1492℃ e 1554℃, il che gioca un ruolo nell'aumentare il punto di fusione nella brasatura del metallo.
Poiché gli elementi attivi nella brasatura sono chimicamente attivi, per evitare reazioni chimiche con l'ossigeno ad alte temperature, la brasatura attiva deve essere eseguita sotto la protezione di un ambiente sotto vuoto o di un'atmosfera inerte e il costo tecnico è elevato e non è adatto per applicazioni su larga scala.
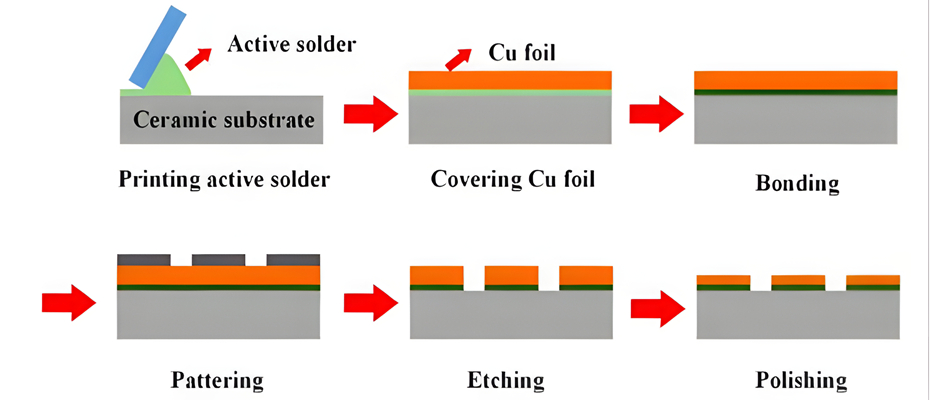