Nel campo dell'industria elettronica, il substrato di allumina è diventato un materiale di base indispensabile per i componenti elettronici grazie al suo eccellente isolamento, stabilità chimica, elevata conduttività termica e buone prestazioni ad alta frequenza. Non svolge solo il ruolo di supporto e dissipazione del calore, ma garantisce anche le prestazioni di isolamento dei componenti elettronici. L'impasto liquido di colata di allumina è la materia prima chiave per la preparazione del substrato ceramico di allumina e la sua composizione e caratteristiche determinano direttamente la qualità e le prestazioni del prodotto finale. Lo scopo di questo articolo è indagare in che modo le caratteristiche della polvere di allumina, tra cui purezza, dimensioni e area superficiale specifica, morfologia e dispersione, influenzano il processo di colata e le prestazioni del substrato ceramico di allumina.
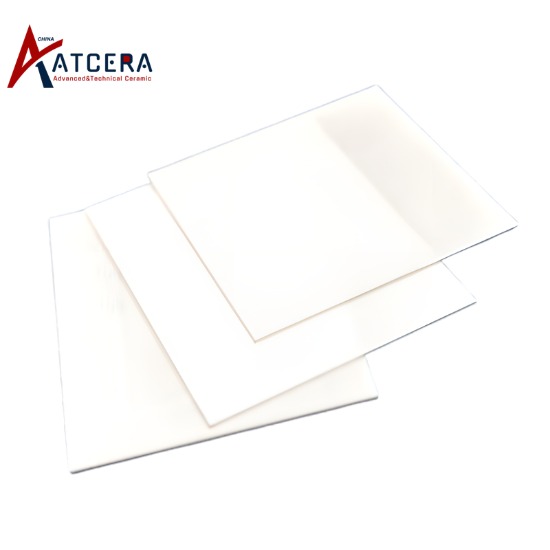
Effetto purezza
La purezza della polvere di allumina è la base della qualità del liquame di colata. Il contenuto di allumina richiesto non è solitamente inferiore al 95% per evitare l'impatto negativo delle impurità sull'aspetto, sul ritiro, sulla microstruttura e sulle prestazioni del prodotto finito. Ad esempio, le polveri di ossido di alluminio contenenti particelle di Fe libere porteranno allo sviluppo di colore all'interno o sulla superficie della ceramica durante il processo di sinterizzazione, formando macchie che non solo influenzano l'aspetto, ma riducono anche le prestazioni di isolamento.
L'effetto della dimensione della polvere e dell'area superficiale specifica
La dimensione della polvere di allumina è controllata nell'intervallo 0,3-1,7μm e l'area superficiale specifica è compresa tra 2-11m²/g, il che ha un impatto importante sulla densità del prodotto finito. La polvere di piccole dimensioni ha un'area superficiale e un'energia superficiale più elevate, che favoriscono la densificazione della pellicola di colata. Tuttavia, una dimensione delle particelle troppo piccola aumenterà la necessità di additivi come disperdenti e leganti, peggiorerà la fluidità dell'impasto liquido, aumenterà il ritiro dalla sinterizzazione e ridurrà la densità di sinterizzazione.
Effetto della morfologia della polvere
La morfologia della polvere di allumina è varia, tra cui sferica, a scaglie, fibrosa e irregolare. Grazie alla superficie liscia e alla buona fluidità, le particelle sferiche contribuiscono a migliorare la densità del prodotto finito. Al contrario, è facile che le particelle non sferiche formino spazi dopo la sinterizzazione, il che influisce sul processo di densificazione.
Ottimizzazione del decentramento
Migliorare la dispersione della polvere nell'impasto liquido è la chiave per garantire la qualità del prodotto finito. Oltre all'aggiunta di disperdenti, il trattamento di modifica della superficie della polvere, come la modifica chimica o il trattamento fisico, può migliorare significativamente la dispersione e le proprietà reologiche dell'impasto liquido, in modo da ottimizzare il processo di colata.
In sintesi, le caratteristiche della polvere di allumina svolgono un ruolo cruciale nel processo di colata della preparazione del substrato ceramico di allumina. Controllando rigorosamente la purezza, le dimensioni, l'area superficiale e la morfologia della polvere e ottimizzando la dispersione, gli indicatori chiave di prestazione come conduttività termica, resistività, costante dielettrica, stabilità chimica e resistenza meccanica del substrato ceramico di allumina possono essere significativamente migliorati. In futuro, con il continuo progresso della scienza dei materiali e della tecnologia di preparazione, lo studio approfondito e la regolazione fine delle caratteristiche della polvere di allumina promuoveranno ulteriormente l'applicazione e lo sviluppo di substrati ceramici di allumina nel campo dei componenti elettronici di fascia alta, e fornire una solida base per lo sviluppo sostenibile dell'industria elettronica.